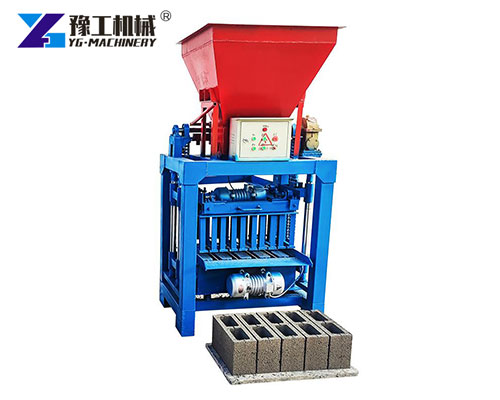
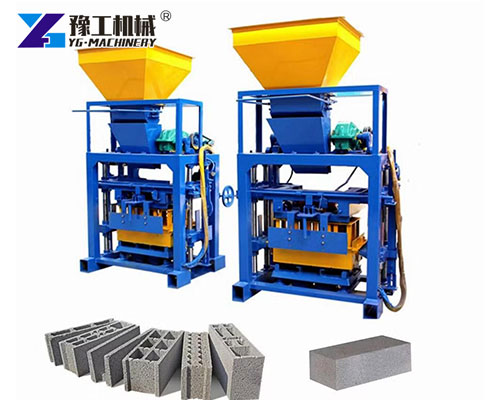
The Hollow Bricks Machine is a specialized construction equipment designed to manufacture hollow bricks—lightweight building blocks that have one or more hollow cavities. These bricks are widely used in modern construction for their thermal insulation, reduced weight, and cost efficiency. The machine automates the process of mixing raw materials (like cement, sand, stone dust, and fly ash), molding, compacting, and curing the bricks into precise shapes.
WhatsApp/WeChat/Phone: 86 138 3715 9132
Hollow Blocks Machine Parameter
Block Name | Size (L*W*H)mm | Molding Cycle | QTY/Mould | QTY/hour | Qty/8hr |
Hollow block | 400*200*200 | 15-20s | 6pcs | 1080-1440pcs | 8640-11520pcs |
Hollow block | 400*150*200 | 15-20s | 7pcs | 1260-1680pcs | 10080-13440pcs |
Hollow block | 400*100*200 | 15-20s | 11pcs | 1980-3640pcs | 15840-21120pcs |
Porous block | 240*115*90 | 15-20s | 15pcs | 2700-3600pcs | 21600-28800pcs |
Standard brick | 240*115*53 | 15-17s | 30pcs | 6300-7200pcs | 50400-57600pcs |
Paver | 225*112.5*60 | 20-25s | 15pcs | 2160-2700pcs | 17280-21600pcs |
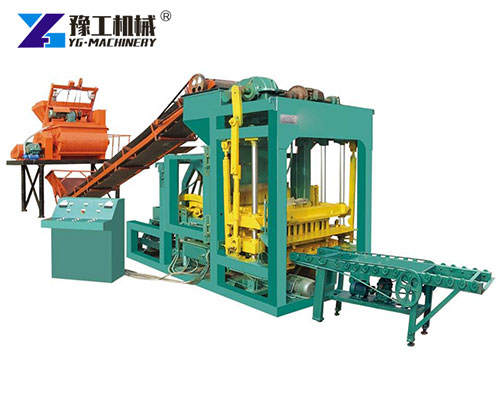
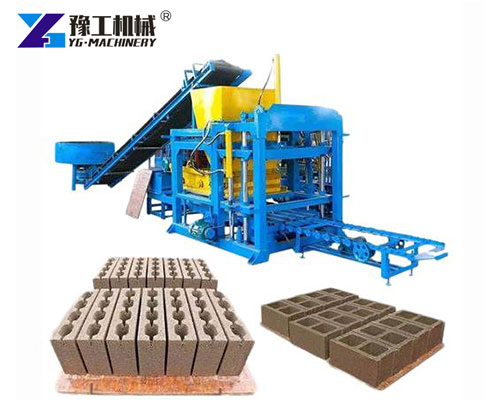
Features of Hollow Bricks Machine
The YG Hollow Bricks Machine incorporates smart features to ensure smooth operation, reduce labor, and maintain consistent output.
Key Features:
- Automated Operation: Supports fully automatic or semi-automatic systems.
- Sturdy Frame: Heavy-duty steel construction ensures machine stability.
- Custom Mold Options: Create various brick sizes and types with ease.
- Hydraulic Pressure System: Delivers strong compression for denser, durable bricks.
- Low Maintenance Design: Simplified structure makes servicing fast and affordable.
These features are ideal for companies aiming to produce hollow bricks continuously without compromising quality.
Hollow Block Making Machine Applications
Hollow blocks produced by our machines are highly versatile and suitable for a broad spectrum of construction applications, making them a preferred choice for modern building:
- Insulation Applications: The hollow structure of these bricks enhances their thermal and acoustic insulation, making them suitable for specific construction needs.
- Residential Buildings: Ideal for constructing exterior and interior walls of houses and apartments, offering excellent thermal insulation and structural stability.
- Commercial Structures: Widely used in the construction of office buildings, shopping centers, and other commercial facilities, providing a cost-effective and efficient building solution.
- Industrial Complexes: Suitable for creating partition walls and non-load-bearing walls in industrial setups, thanks to their lightweight nature and soundproofing qualities.
- Boundary Walls and Fencing: An excellent choice for building durable and aesthetically pleasing boundary walls and fences around properties.
- Partition Walls: Their lightweight nature makes them perfect for the quick and easy construction of internal partition walls, reducing overall structural load.
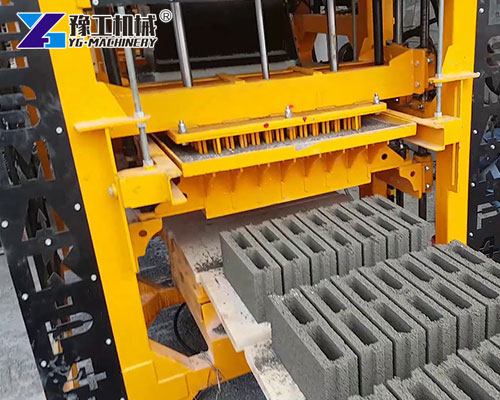
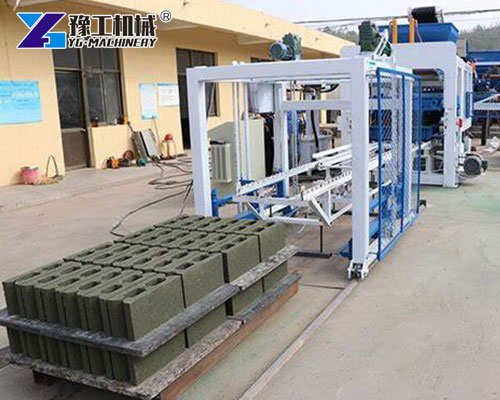
Advantages of Using Hollow Bricks
Hollow bricks made with a Hollow Bricks Machine offer multiple advantages over traditional solid bricks, making them a smart choice for modern construction.
- Lightweight Structure: Reduces overall building weight and load on foundations.
- Thermal and Sound Insulation: Hollow spaces trap air and minimize heat and noise transfer.
- Lower Raw Material Usage: Saves cement, sand, and other inputs.
- Cost-Effective: Faster construction leads to labor and time savings.
- Eco-Friendly: Reduces carbon footprint due to less material consumption.
Their practical and environmental advantages make hollow bricks highly desirable in sustainable construction.
How to Select the Right Hollow Bricks Machine
Choosing the appropriate Hollow Bricks Machine for your business requires careful consideration of several factors to ensure it meets your production needs and operational efficiency goals:
- Budget: While cost is a factor, prioritize value. A slightly higher initial investment in a quality machine can lead to greater long-term savings through higher efficiency, lower maintenance, and superior product quality.
- Production Capacity: Determine your required hourly or daily brick output. Machines come in various capacities, from smaller manual models to fully automatic high-volume systems. Match the machine’s capacity with your project scale.
- Automation Level: Decide between manual, semi-automatic, or fully automatic machines. Fully automatic machines offer higher output and less labor but come at a higher initial investment. Semi-automatic options provide a balance of cost and efficiency.
- Raw Material Compatibility: Ensure the machine is compatible with the raw materials you intend to use (e.g., cement, sand, fly ash, quarry dust, aggregates). Different machines may have specific requirements for material composition and consistency.
- Mold Versatility: If you plan to produce various sizes and types of hollow bricks or other blocks (like those from a Hollow Block Making Machine), look for a machine with an easy and quick mold-changing system.
- Durability and Build Quality: Investigate the construction materials and manufacturing standards. A machine made with high-quality steel and robust components will ensure a longer lifespan and less downtime.
- After-Sales Service and Support: Verify the manufacturer’s reputation for after-sales support, including spare parts availability, technical assistance, and training. This is crucial for minimizing operational disruptions.
- Energy Efficiency: Consider the machine’s power consumption. An energy-efficient model will lead to significant savings on electricity bills over time.
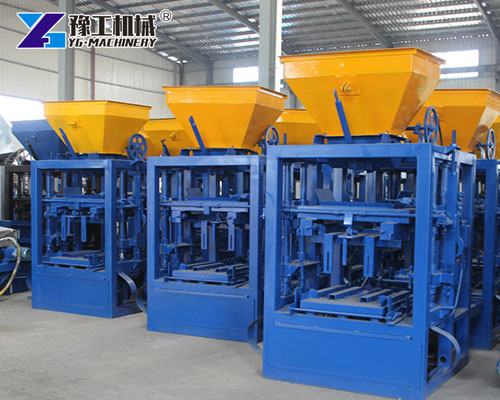
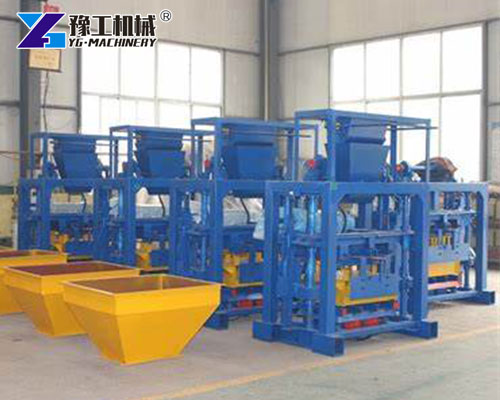
Operation Guide for Hollow Bricks Machine
Proper operation of the Hollow Bricks Machine ensures consistent quality and extends machine life. Follow these steps for smooth production:
- Prepare the Mix: Combine raw materials like cement, fly ash, sand, and water.
- Load the Hopper: Transfer the mixture into the machine’s hopper.
- Activate the Machine: Start the molding and compression process.
- Demold and Cure: Allow bricks to dry and cure before stacking or transporting.
Operational Tips:
- Check the hydraulic fluid and motor status regularly.
- Clean molds after each cycle to avoid product defects.
- Train workers on safety protocols and emergency procedures.
A systematic approach reduces production delays and ensures brick uniformity.
FAQ About Hollow Bricks Machine
1. What Is a Hollow Bricks Machine and What Types of Bricks Can It Make?
A hollow brick machine is equipment designed to produce hollow bricks, widely used in construction. Depending on the mold, it can manufacture various sizes of hollow bricks, solid bricks, perforated bricks, and even paving blocks.
2. How Many Bricks Can the Machine Produce Per Day?
Production capacity varies by model and automation level:
- Manual type: 1,000–2,500 bricks/day
- Semi-automatic type: 3,000–6,000 bricks/day
- Fully automatic type: up to 10,000–25,000 bricks/day or more
3. How Many Workers Are Needed to Operate the Machine?
- Manual machines typically require 3–5 workers.
- Semi-automatic models need 2–3 operators.
- Fully automatic machines can be managed by just 1–2 trained staff.
4. What Raw Materials Can Be Used?
Common materials include:
- Cement
- River sand or crushed stone powder
- Fly ash
- Slag powder
- Water
Some models can also use biomass ash, construction waste, or recycled aggregates.
5. Can the Molds Be Changed for Different Brick Types?
Yes, molds can be changed easily to produce different sizes and shapes. The changeover process takes about 5–20 minutes and requires no special tools.
6. Do the Bricks Need to Be Fired in a Kiln?
No. The bricks made by a hollow brick machine are non-fired. They gain strength through high-pressure molding and natural curing or steam curing, making the process energy-efficient and eco-friendly.
7. How Much Space Is Required for a Hollow Brick Production Line?
Depending on the model:
- Manual: around 50–100 sqm
- Semi-automatic: around 150–300 sqm
- Fully automatic: minimum 400 sqm (including curing area and raw material storage)
8. What Is the Power Requirement? Is It Energy Intensive?
Main motor power ranges from 7.5–15 kW, while a full production line may need 20–60 kW, depending on the level of automation. Newer models with frequency inverters are more energy-efficient.
9. How to Maintain the Machine for Long-Term Use?
- Clean leftover material from molds and vibration plates daily
- Lubricate moving parts regularly (bearings, guides)
- Check the electrical and control systems periodically
- Monitor the hydraulic system for leaks and overheating
- Inspect mold wear and repair or replace as needed
10. Is Installation and After-Sales Support Provided?
Reliable manufacturers (like YG Machinery) usually offer:
- On-site or remote installation assistance
- Operator training
- Free spare parts during the warranty period
- Lifetime technical support and service
WhatsApp/WeChat/Phone: 86 138 3715 9132