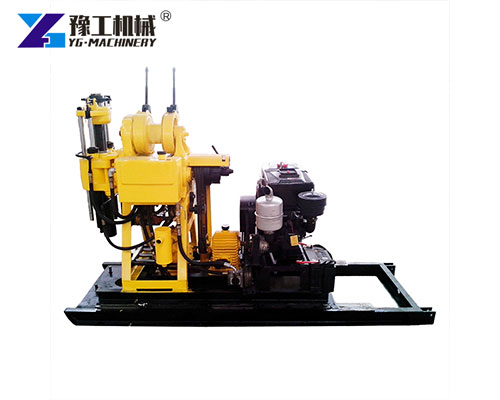
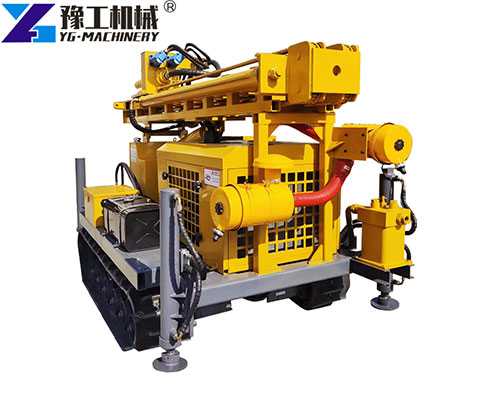
Core drilling rigs utilize wireline diamond technology for surface and underground mineral exploration in geological, metallurgical, coal, nuclear, and hydrogeological sectors. These rigs feature adaptable configurations with optional hydraulic clamping systems and automated rod-changing capabilities for efficient core sampling operations in diverse terrains and industrial applications. WhatsApp/WeChat/Phone/Skype+86 138 3715 9132
Technical Data for Core Drilling Equipment
Model | XY-3 | XYD-3 | XYX-3 |
Drilling Depth (m) | 600 | 600 | 600 |
Open Drilling Diameter (mm) | 325 | 325 | 325 |
Final Hole Diameter(mm) | 75 | 75 | 75 |
Drill Pipe Diameter(mm) | 42-60 | 42-60 | 42-60 |
Drill Pipe Inclination (°) | 90-75 | 90-75 | 90-75 |
Power (kW) | YN27/39 | YN33GBZ/65 | YN27/39 |
Weight (kg) | 1800 | 6200 | 3600 |
Dimensions(mm) | 2600*900*1750 | 4500*200*2700 | 2900*2560*3300 |
Components of the Core Drilling Rig
The Core Drilling Rig consists of several key components:
- Drill Bit: This is the part that comes into direct contact with the ground. It is made of hard materials such as diamond or carbide to cut through the rock effectively.
- Drill Rods: These are long, cylindrical pipes that connect the drill bit to the rig. They transfer the rotational and downward force from the rig to the drill bit.
- Power Unit: It provides the energy needed to operate the rig. This can be a diesel engine, an electric motor, or a hydraulic system.
- Hoisting System: Used to raise and lower the drill rods and the drill bit. It ensures smooth and controlled movement during the drilling process.
- Control Panel: Allows the operator to control various functions of the rig, such as the speed of rotation, the pressure applied to the drill bit, and the movement of the hoisting system.
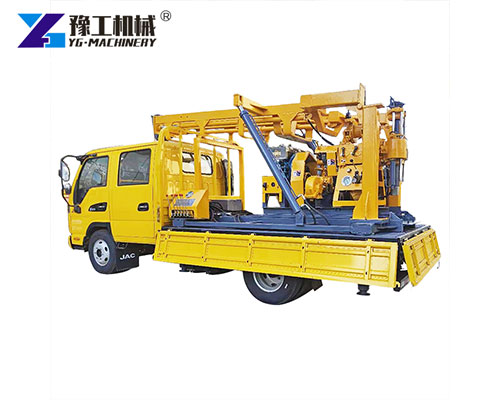

Core Drilling Rig Features
High Precision
Engineered with advanced wireline diamond technology, the rig ensures precise extraction of core samples, delivering representative subsurface data critical for geological analysis.
Versatility
Designed for diverse terrains, it operates seamlessly in hard rock, soft soil, and even underwater environments, supporting exploration across mining, hydrogeology, and energy sectors.
Durability
Constructed with high-grade materials, the rig withstands extreme conditions at mining and exploration sites, ensuring long-term performance in harsh operational settings.
Operational Efficiency
Optimized for speed and energy utilization, it minimizes downtime and energy loss while completing drilling tasks swiftly. Automated features like hydraulic clamping and rod-changing systems further enhance productivity, reducing project timelines and costs.
User-Centric Design
Simplified controls and intuitive operation lower the skill barrier for operators, enabling efficient workflows without compromising safety or precision.

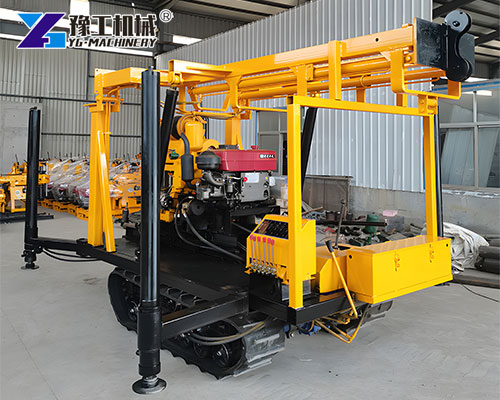
Types of Core Drilling Rigs
Surface Core Drilling Rigs
Application: Designed for surface geological exploration, with depth ranges from 50m to over 1500m.
Technology: Typically use wireline diamond coring systems with high automation. Mountable on trucks, crawlers, or trailers.
Scenarios: Mineral prospecting, hydrological surveys, and engineering geology.
Underground Core Drilling Rigs
Application: Compact rigs for mine shafts or tunnels.
Features: Small size, high mobility, and adaptability to confined spaces for ore tracking or reserve verification.
Hydraulic-Driven Rigs
Advantages: Full hydraulic systems enable high power and precise control, ideal for deep hard-rock drilling.
Features: Often equipped with automated rod changers and hydraulic clamps for efficiency.
Portable Lightweight Rigs
Use: Shallow-depth exploration (50m–300m), suitable for rugged terrain (mountains, forests).
Design: Modular assembly for easy transport via manual or small machinery.
Fully Automated Deep-Hole Rigs
Function: Integrated smart control systems enable unmanned operations for ultra-deep holes (1500 m+).
Technology: Real-time data monitoring and remote management reduce manual intervention.
How to Use a Core Drilling Rig
Using a Core Drilling Rig involves the following steps:
Site Preparation
Clear the drilling site of any obstacles, level the ground if necessary, and mark the drilling location.
Rig Setup
Transport the rig to the site and assemble it according to the manufacturer’s instructions. Connect all the components and ensure they are properly installed.
Drilling Operation
Start the power unit and adjust the parameters on the control panel, such as the rotation speed and the downward pressure. Lower the drill bit to the ground and start the drilling process. Periodically remove the drill rods to retrieve the core samples.
Rig Disassembly and Cleanup
Once the drilling is completed, disassemble the rig, clean all the components, and store them properly for future use.
Why Choose YG Core Drilling Rigs
When it comes to Core Drilling Rigs, YG is a top choice for several reasons:
- Quality Assurance: YG uses high-quality materials and advanced manufacturing techniques to ensure the durability and reliability of its drilling rigs.
- Customization: We can customize the drilling rig according to the specific requirements of the customers, such as the drilling depth, the diameter of the core samples, and the type of terrain.
- Technical Support: YG provides comprehensive technical support to its customers, including installation guidance, training, and after-sales service.
- Competitive Pricing: YG’s core drilling rig price is competitive without compromising on quality, offering excellent value for money.
WhatsApp/WeChat/Phone/Skype+86 138 3715 9132