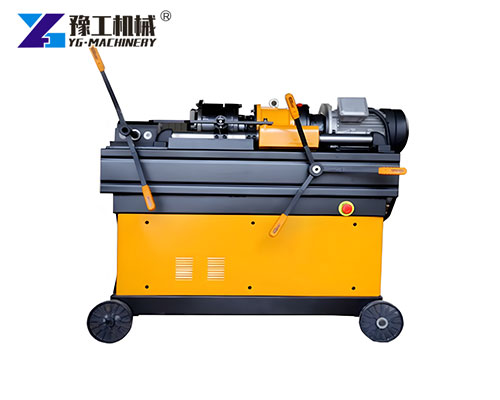
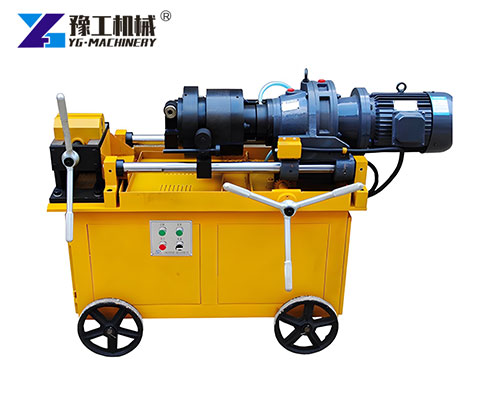
The rebar thread rolling machine is a specialized piece of equipment designed to create threads on the ends of steel reinforcement bars. Unlike traditional methods like cutting or welding, which can weaken the bar or require extensive labor, thread rolling uses a cold-forming process to shape threads by pressing dies or rollers against the bar’s surface. This process doesn’t remove material but instead deforms it, resulting in threads that are stronger than the original bar.
There are different types of thread rolling machines, such as the CNC thread rolling machines and the parallel thread rolling machine. These machines have their unique features and applications, but they all share the common goal of producing high-quality threads on rebars. WhatsApp/WeChat/Phone +86 138 3715 9132
Parameters of Rebar Thread Rolling Machine for sale
Model | YGS-40 | YGT-40 | YGA-40 |
Processing diameter range | 16-40mm | 16-40mm | 16-40mm |
Thread rolling length | 0-80mm | 0-80mm | 0-100mm |
Power voltage | 4kw/380v 50hz | 4kw/380v 50hz | 7.5kw/380v 50hz |
Working efficiency | 15s/forming | 8s/forming | One-touch auto forming |
Machine weight | 320kg | 350kg | 400kg |
Machine size | 115*50*106cm | 110*60*130cm | 126*70*106cm |
Type | Standard type | Upgrade type | Full automatic type |
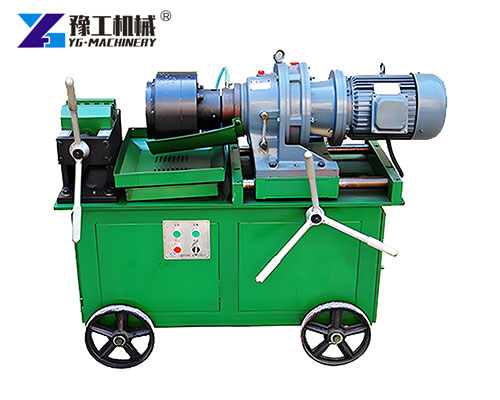
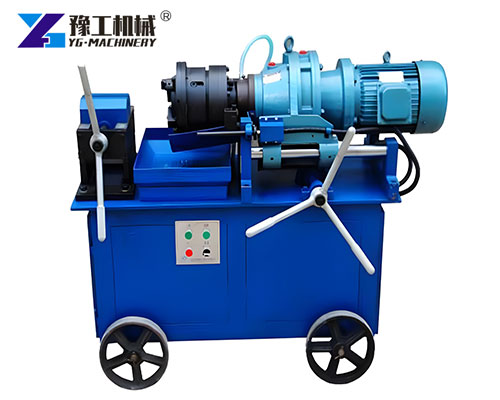
Applications of the Rebar Rolling Machine
- Construction Projects: In building construction, rebars with threaded ends are used to connect different parts of the reinforcement framework. This ensures a strong and reliable structure. For example, in high-rise buildings, the use of properly threaded rebars can withstand high loads and seismic forces.
- Bridges: Bridges require a strong and stable reinforcement system. The rebar threading equipment helps in creating threads on rebars used in bridge piers, beams, and decks, enhancing the overall strength and safety of the bridge.
- Industrial Structures: Factories, warehouses, and other industrial buildings also rely on threaded rebars for their structural integrity. The Rebar Thread Rolling Machine ensures that the rebars used in these structures meet the required standards.
- Prefabrication Yards: Factories that produce precast concrete elements (like wall panels or beams) use rebar thread rolling machines to mass-produce threaded bars. These pre-threaded components are then shipped to sites for quick assembly, reducing on-site labor and delays.
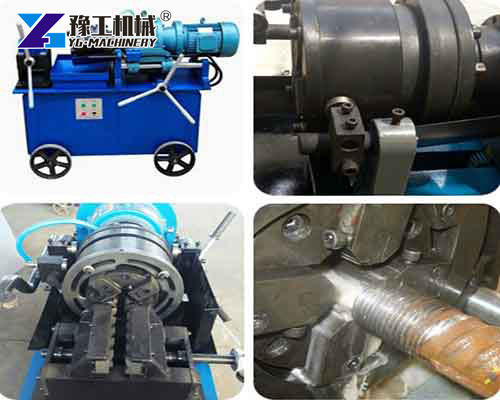
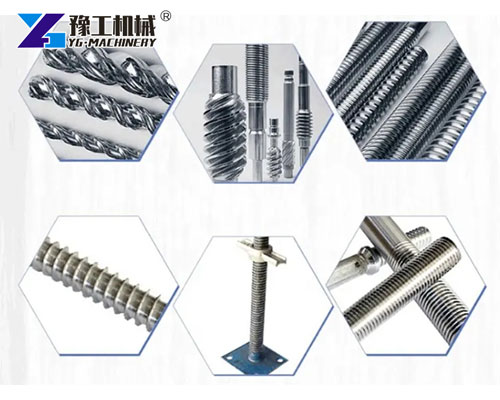
Thread Rolling vs. Traditional Threading
Traditional Threading (Cutting): Involves using a cutting tool to remove material and create threads. This weakens the bar at the thread site and makes it more prone to defects like uneven threads.
Cold Thread Rolling: Forms threads by deforming the steel without material removal, enhancing strength and durability. It’s faster, more precise, and ideal for high-grade rebars used in critical structures.
Features of the Thread Rolling Equipment
Modern thread rolling machines feature advanced capabilities:
- High Precision: Ensure accurate thread dimensions for secure rebar connections, vital for structural stability.
- Efficiency: Automatic models streamline threading, reducing production time and boosting productivity.
- Versatility: Adapt to various rebar diameters and types, ideal for diverse construction needs.
- Durability: Built with robust materials to withstand heavy use in harsh environments.
- Time-Saving: Sensor-guided alignment, automatic die adjustment, and pre-programmed settings cut processing time by up to 30%, minimizing errors.
- User-Friendly Interfaces: Touchscreens enable easy setting of thread specs; digital presets and real-time monitoring enhance workflow management.
- Portability: Compact, wheeled, or foldable designs allow effortless on-site transport, fitting tight spaces in high-rise or infrastructure projects. The thread roller machine comes with several advanced features:
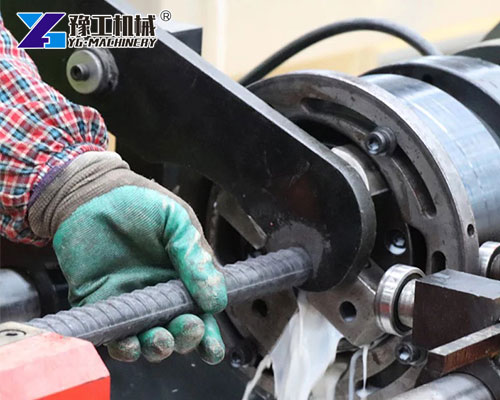
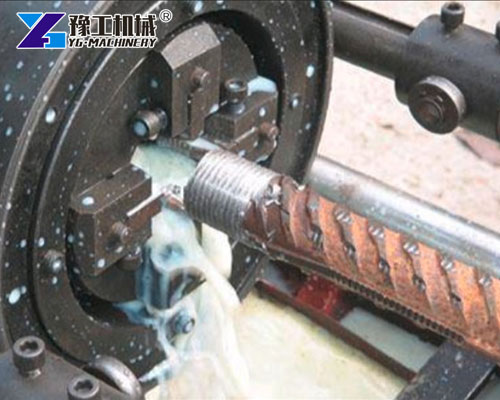
Working Principle of Rebar Rolling
The working principle of a rebar thread rolling machine involves two key stages: rib peeling and cold thread rolling. First, the ribbed surface of the rebar is peeled to create a smooth cylindrical section. Then, rotating dies or rollers apply pressure to form threads through cold forming, a process that strengthens the steel by aligning its grain structure without heating. This ensures precise thread pitch/depth, maintains the rebar’s mechanical properties, and produces durable threads resistant to tensile and shear forces for reliable structural connections.
How to Choose a Rebar Thread Rolling Machine
1. Bar Diameter Range
Check the machine’s supported diameter range to match your project needs. For example, a residential project using 12–25mm rebars doesn’t require a machine that handles 50mm bars, but a bridge project might need the full range.
2. Power Source
Single-Phase Power: Suitable for small sites or prefabrication yards with standard electrical access.
Three-Phase Power: Offers more consistent power for heavy-duty machines processing large bars, ideal for industrial use.
3. Threading Speed and Capacity
Look for machines rated by production capacity. Higher speed is crucial for a tight deadline, but may come with a higher initial cost.
If you have a large-scale project, an automatic thread rolling machine may be more suitable as it can increase efficiency and reduce labor costs.
4. Build Quality and Tool Life
Machines with hardened steel rollers and tungsten carbide peeling blades last longer, even with high-volume use. Check for anti-corrosion coatings on metal parts, especially if working in coastal or wet environments.
5. After-Sales Support
Compare the prices of different machines and also consider the after-sales service provided by the manufacturer. A reliable manufacturer should offer technical support and spare parts.
Maintenance Tips for Rebar Thread Rolling Machine
Proper maintenance of the Rebar Thread Rolling Machine is essential to ensure its long-term performance:
- Regular Cleaning: Keep the machine clean to prevent the accumulation of dirt and debris, which can affect its operation.
- Lubrication: Lubricate the moving parts of the machine regularly to reduce friction and wear.
- Inspection: Periodically inspect the dies and other key components for wear and damage. Replace them if necessary.
- Electrical System Check: Check the electrical system of the machine to ensure its safety and proper functioning.
Why choose YG Machinery?
YG Machinery is a well-known manufacturer of Rebar Thread Rolling Machine. They have years of experience in the industry and are committed to providing high-quality equipment. YG Machinery also offers excellent after-sales service, including technical support and spare parts supply. What is the machine’s price? Please leave your inquiry below or contact us via WhatsApp 0086 138 3715 9132.