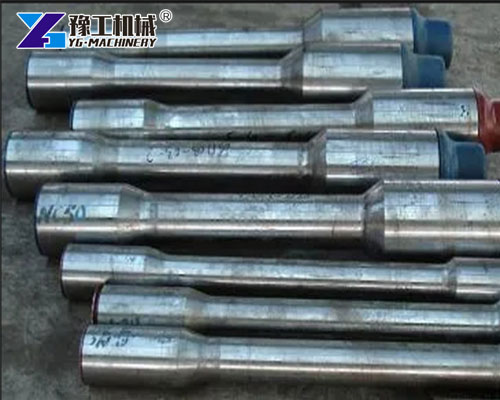
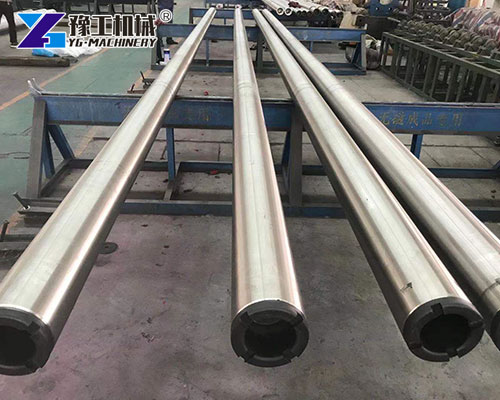
What Are Drill Collars?
Drill collars are thick-walled steel tubes used in drilling operations to add weight to the drill bit, ensuring it cuts effectively through rock formations. They are installed at the lower part of the drill string, just above the drill bit, and help maintain the desired vertical trajectory of the borehole. Unlike standard drill pipes, drill collars are not hollow for fluid passage but solid and much heavier.
Their primary function is to apply weight on bit (WOB) while reducing the risk of unintentional deviation and vibrations, especially in hard-rock drilling environments.
WhatsApp/WeChat/Phone: 86 138 3715 9132
Core Functions of Drill Collars
Using Drill Collars for Sale in your project ensures mechanical stability and precise drilling performance. Their main roles include:
- Delivering WOB (Weight on Bit): Essential for effective rock penetration.
- Maintaining Hole Straightness: Prevents drill string buckling and borehole deviation.
- Minimizing Vibrations: Reduces bit bounce and tool fatigue, improving service life.
- Balancing the Drill String: Optimizes load distribution across the drilling system.
- Supporting Other BHA Components: Works alongside stabilizers, subs, and reamers.
These functions make drill collars indispensable in directional, vertical, and extended-reach drilling.
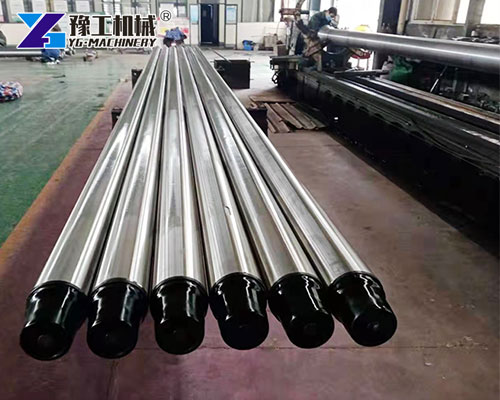
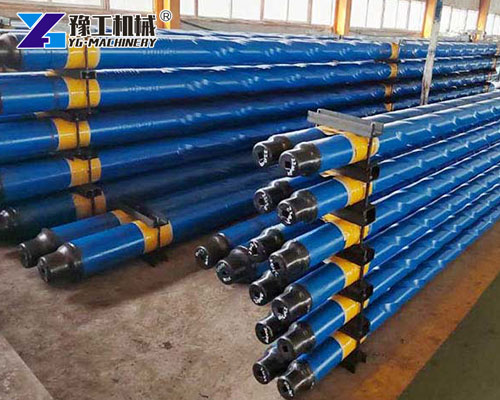
Technical Features of Drill Collars
The quality and design of drill collars are key to operational safety and drilling efficiency. Standard features include:
- Material: Typically made from AISI 4145H alloy steel, known for toughness and fatigue resistance.
- Surface Finish: Precision-ground to reduce differential sticking in the borehole.
- Threaded Ends: Machined with API or premium threads to match other BHA tools.
- Spiral Grooves (optional): Help reduce wall contact area and differential sticking.
- Non-Magnetic Options: Made from stainless alloys for use in MWD/LWD assemblies.
Advanced collars also offer stress relief features and hardbanding for enhanced wear resistance.
Types of Drill Collars by Function and Size
When evaluating Drill Collars for Sale, it’s important to understand the different types available:
By Function
- Standard Steel Drill Collars: Heaviest and most widely used type for general drilling.
- Spiral Drill Collars: Designed with helical grooves to minimize sticking in deviated holes.
- Non-Magnetic Drill Collars: Used with directional tools to avoid magnetic interference.
- Slick Drill Collars: Smooth outer surface, ideal for vertical wells.
By Size
- OD (Outside Diameter): Typically ranges from 3 1/8” to 11”. Larger diameters offer more weight.
- Length: Usually available in 31 ft to 32 ft. Custom lengths are also available.
- Thread Type: Common connections include NC38, NC50, or custom threads based on rig setup.
Each type supports specific drilling objectives, ensuring better weight control and borehole quality.
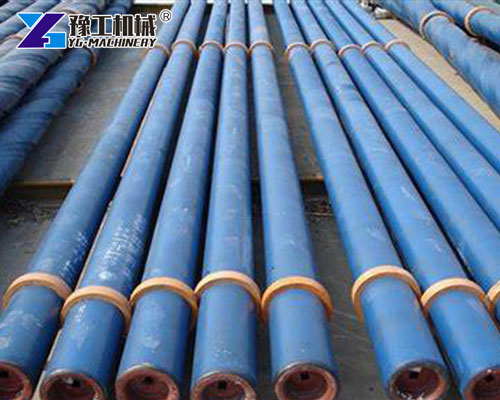
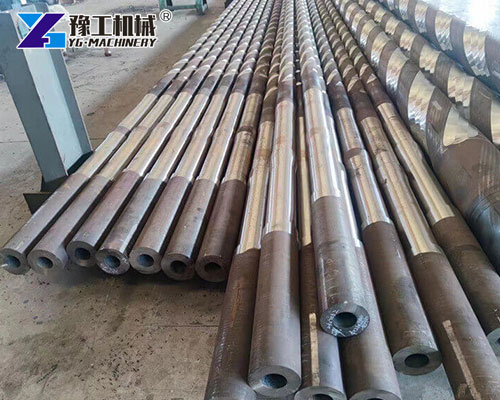
Selection Factors for Drill Collars for Sale
Choosing the right Drill Collars for Sale involves evaluating key drilling and budgetary conditions:
- Well Depth: Deeper wells require more or heavier drill collars to apply the proper weight on bit (WOB).
- Formation Type: Hard or abrasive rocks benefit from high-weight collars; soft formations may require lighter options.
- Drilling Method: Vertical wells use slick collars; directional wells need spiral or non-magnetic types.
- Rig Capabilities: Total collar weight must match the rig’s load rating.
- Tool Compatibility: Match thread types and outer diameters (OD) to stabilizers, subs, and bits.
- Cost: While heavier or specialty collars may cost more, they often improve overall efficiency.
Correct selection improves the rate of penetration (ROP), safety, and drilling accuracy.
Practical Use of Drill Collars in the Field
Drill collars are installed directly above the drill bit and serve as a key component of the bottom hole assembly (BHA). Typical field usage includes:
- Vertical Drilling: Providing downward force while ensuring the hole remains straight.
- Directional Drilling: Used with measurement-while-drilling (MWD) tools to maintain trajectory.
- Reaming and Stabilization: When paired with stabilizers, it helps reduce borehole wall irregularities.
- Weight Distribution: Prevents drill pipe buckling by acting as a counterbalance during rotation.
Operators must monitor torque, WOB, and vibration levels to adjust collar configuration as drilling progresses.
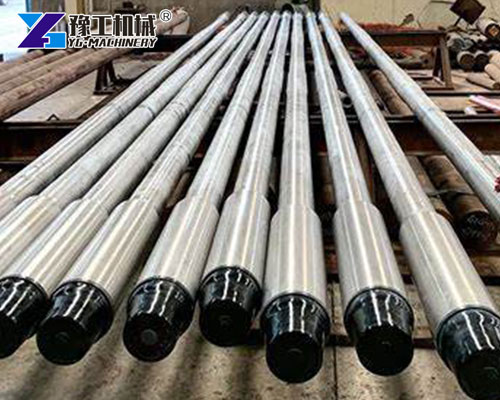
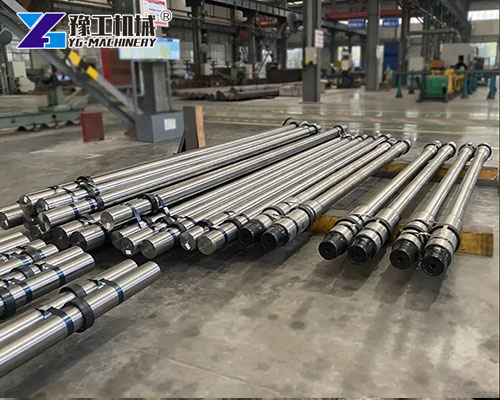
Frequently Asked Questions About Drill Collars
- Q1: How long do drill collars typically last?
A: With proper handling and inspection, collars can last for multiple projects. Regular ultrasonic testing helps detect internal flaws. - Q2: Can I use magnetic collars with MWD tools?
A: No. For directional drilling with sensitive instruments, use non-magnetic collars to avoid data interference. - Q3: What’s the difference between slick and spiral drill collars?
A: Spiral collars have grooves to reduce wall contact; slick collars have smooth surfaces and are used in stable, vertical wells. - Q4: How many drill collars should I use?
A: It depends on the required WOB. Most setups need 4000–6000 lb per inch of bit diameter, divided among several collars. - Q5: Do I need to replace a collar if the threads are damaged?
A: Yes. Thread integrity is crucial for connection strength and should be checked before every run.
WhatsApp/WeChat/Phone: 86 138 3715 9132