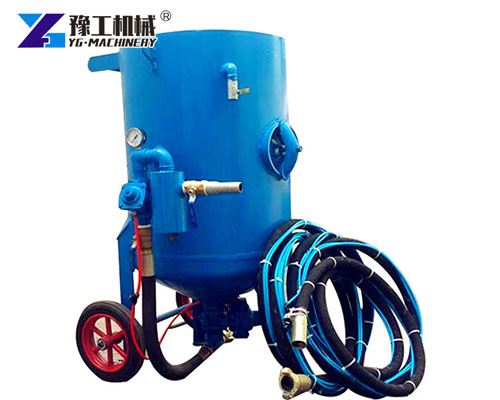
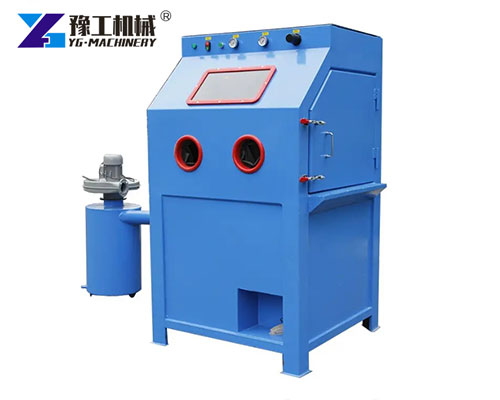
What Is A Wet Blasting Machine?
A Wet Blasting Machine is a surface preparation tool that uses a mixture of water and abrasive media to clean, polish, or prepare surfaces. Unlike dry blasting, wet blasting significantly reduces dust and heat generation, making it ideal for fine finishing and delicate components.
The water-based slurry process yields smoother results with less surface damage, making it ideal for the aerospace, automotive, medical device, and mold-making industries.
WhatsApp/WeChat/Phone: 86 138 3715 9132
Sand Blasting Machine Main Parameters:
Machine models | YG400 | YG500 | YG600 | YG700 | YG800 | YG900 | YG1000 |
Diameters(mm) | 400 | 500 | 600 | 700 | 800 | 900 | 1000 |
Height(mm) | 1150 | 1150 | 1150 | 1250 | 1700 | 2000 | 2000 |
Volume(cubic meter) | 0.26 | 0.26 | 0.26 | 0.3 | 0.6 | 0.8 | 1 |
Pressure(Mpa) | 0.4-8 | ||||||
Air consumption(cubic meters per minute) | 3 |
Key Features of the Wet Blasting Machine
Modern Wet Blasting Machines are designed with advanced features to improve productivity, ease of use, and safety.
- Stainless Steel Construction: Corrosion-resistant and long-lasting
- Adjustable Nozzles: Customizable blasting angle and intensity
- Fully Enclosed Cabinet: Keeps the workspace clean and contained
- Integrated Lighting: Clear visibility during operation
- Heavy-Duty Pump System: Stable slurry flow and pressure
- Touchscreen Control Panel: User-friendly and precise settings
Some models also feature automatic turntables, robotic arms, or multi-gun setups, which are ideal for high-volume production environments.
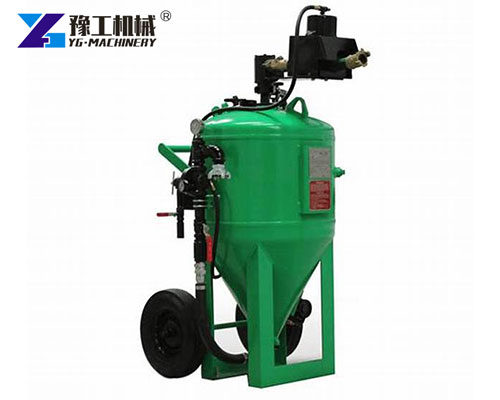
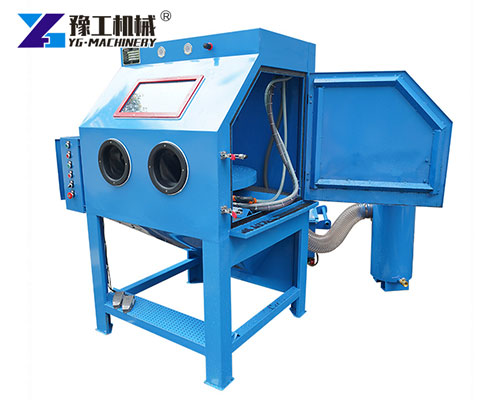
Main Applications of Wet Blasting Machines
Wet Blasting Machines are widely used in industrial sectors where precision surface treatment is critical. Typical applications include:
- Rust and scale removal from metal parts
- Surface preparation before painting or coating
- Cleaning delicate components such as turbine blades or injection molds
- Deburring aluminum and magnesium parts
- Matte finishing for stainless steel and glass
Thanks to its low-abrasion nature, wet blasting is particularly useful where dimensional accuracy and surface integrity are essential.
How Does a Wet Blast Cabinet Work?
A Wet Blast Cabinet operates by mixing water with abrasive media to create a slurry. This slurry is then pumped through a nozzle using compressed air, which propels it onto the workpiece.
Key components of the system include:
- Slurry Pump: Circulates the water-abrasive mix
- Nozzle System: Controls the pressure and spray pattern
- Cabinet Chamber: An Enclosed area that contains the blasting process
- Filtration & Drainage: Separates sludge and recycles water
- Gloves and View Window: Allows safe operator control
This process is more controlled and safer than dry blasting, especially when dealing with hazardous materials or fragile parts.
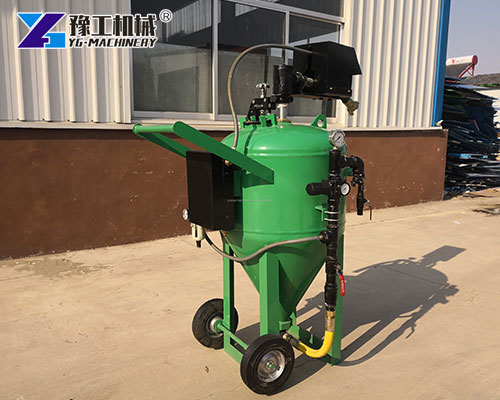
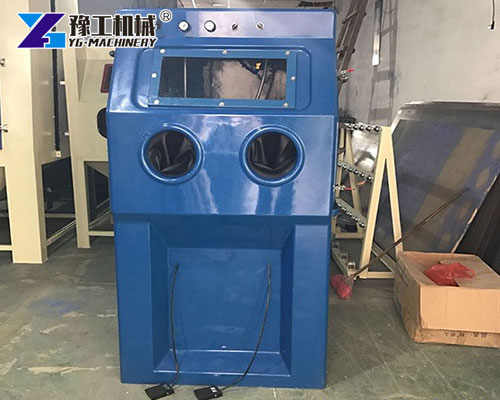
Advantages of Using a Wet Blast Cabinet for Sale
When compared with traditional sandblasting or dry abrasive methods, a Wet Blast Cabinet for Sale offers several operational and environmental benefits:
- Low Dust Output: Safer for workers and the environment
- Surface Protection: Less aggressive, ideal for precision work
- Better Finish Quality: Smooth satin surface with minimal roughness
- Cooling Effect: Water prevents overheating and warping
- Longer Media Life: Reduced breakdown of abrasives
This makes wet blast cabinets suitable for both industrial-scale operations and sensitive lab work.
Buying Guide: Wet Blasting Machine for Sale
If you’re planning to invest in a Wet Blasting Machine for Sale, consider the following criteria to ensure the machine fits your needs:
- Workpiece Size: Choose the cabinet dimensions that accommodate your largest part
- Application Type: Cleaning, finishing, or prep work—each may need different nozzle types or media
- Production Volume: For continuous use, select a high-duty cycle machine
- Abrasive Compatibility: Ensure the machine supports your preferred media
- Maintenance Access: Opt for designs with easy filter and pump access
- Power Supply & Air Requirements: Match the machine with your facility’s specs
Always consult the YG Machinery manufacturer for full specifications, especially when ordering custom configurations.
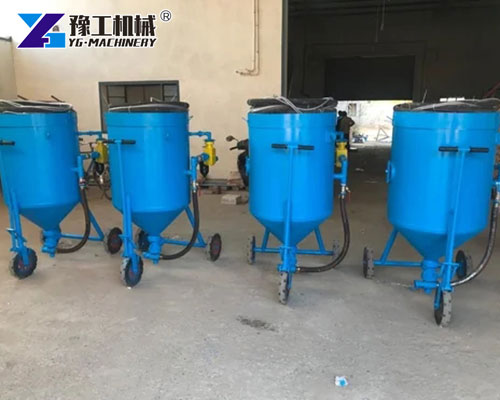
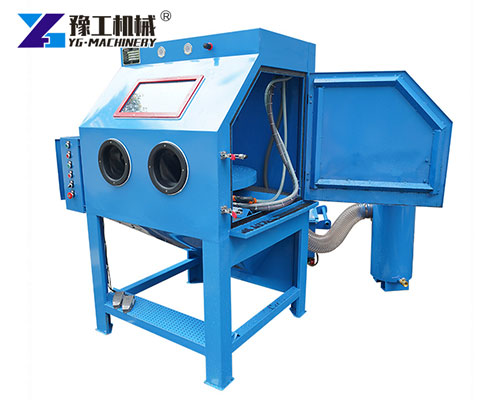
How to Choose the Right Abrasive Media
The performance of a Wet Blasting Machine largely depends on selecting the right abrasive media. Factors to consider include:
- Surface Material: Aluminum, steel, glass, plastic
- Desired Finish: Matte, satin, or mirror-like
- Cleaning Depth: Light cosmetic or deep oxide removal
- Abrasive Type Options:
- Glass Beads – for smooth finishing
- Aluminum Oxide – aggressive cutting
- Silicon Carbide – a very hard material
- Plastic Media – for electronics and soft metals
For best results, test different media under real working conditions.
Frequently Asked Questions About Wet Blasting Machines
- Q1: What’s the difference between wet and dry blasting?
Wet blasting uses water and abrasive together, which reduces dust and results in smoother finishes. Dry blasting is faster but generates more dust and heat. - Q2: Is a Wet Blasting Machine safe for aluminum parts?
Yes, it’s ideal. The water cushion reduces the risk of warping or over-etching aluminum surfaces. - Q3: How often should the slurry be changed?
This depends on usage and media breakdown, but generally every 50–100 operating hours. - Q4: Can a Wet Blasting Machine clean internal cavities?
Yes, with the proper nozzle design and part orientation, internal surfaces can be effectively treated. - Q5: Do you offer portable or bench-top models?
Yes, models are available for different workspace needs—from compact bench units to full industrial cabinets.
WhatsApp/WeChat/Phone: 86 138 3715 9132